Energy Conservation with Variable Speed Controllers in Boiler Houses
Abstract
This explores the impact of the excess air ratio on the efficiency of a water tube boiler system capable of producing 55 tons of steam per hour at 245 °C and 20 bar pressure. The boiler’s combustion air is supplied by a fan powered by a 30 kW induction motor running at 1450 rpm. The fan motor operating at full speed supplied excessive airflow at low loads, leading to high exhaust gas temperatures and significant thermal and electrical energy losses. A variable speed drive (VSD) was implemented to reduce the fan motor speed from 1450 rpm to 400 rpm. This adjustment lowered stack temperature from 195 °C to 145 °C, boosting boiler efficiency by 2.5% and saving 8000 kWh of electrical energy per month. The paper outlines a method for energy conservation in boiler houses using VSDs, evaluates energy losses linked to excess air rates, and analyzes the associated costs.
Introduction
The consequences of greenhouse gas emissions—rising global temperatures, extreme weather events, and economic instability—are well-documented. As global reliance on fossil fuels continues to grow, so do emissions and the risks of climate change. International initiatives like the 1992 Rio Earth Summit and the Kyoto Protocol have set targets to reduce greenhouse gas emissions, prompting nations to adopt strategies to meet these goals.
Two critical challenges emerge for industries reliant on boilers: rising energy costs and the environmental impact of greenhouse gas emissions. The excess air ratio heavily influences boiler efficiency, which measures the system’s ability to convert fuel into steam. While some excess air is necessary to ensure complete combustion and safe operation, too much leads to unnecessary heating and energy losses. This study focuses on optimizing the excess air ratio to improve boiler efficiency, reduce energy waste, and minimize emissions.
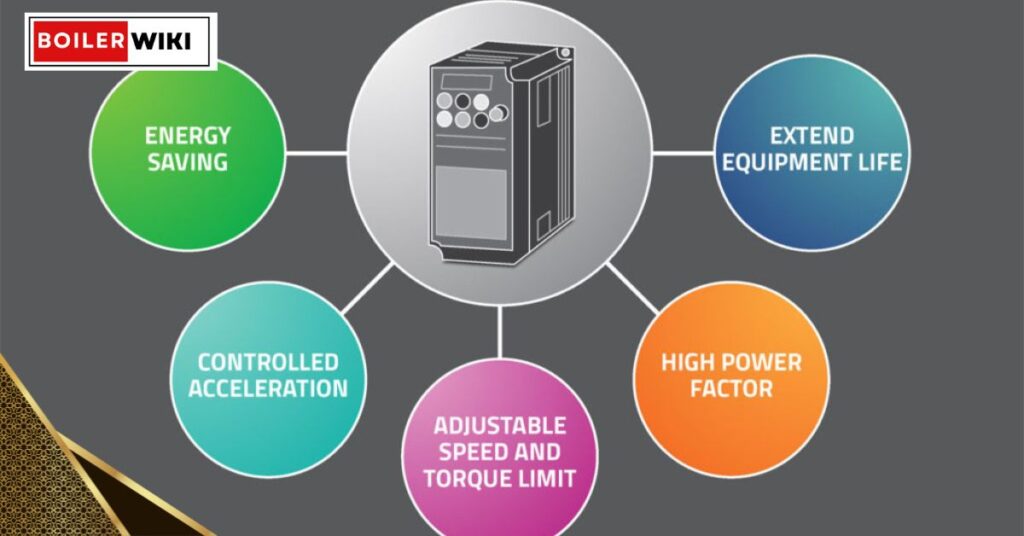
Boiler efficiency depends heavily on combustion control. Modern burners maintain optimal air-to-fuel ratios across varying loads, but wear and improper adjustments can cause inefficiencies. This study investigates the effects of excess air on boiler performance and demonstrates how variable speed drives (VSDs) can optimize airflow, reduce energy losses, and enhance system efficiency.
The research was conducted on a water tube boiler installed in a tire manufacturing plant in Izmit, Turkey. The boiler, which can produce 55 tons of steam per hour at 245 °C and 20 bar pressure, supplies steam for tire-curing processes. Steam demand fluctuates based on production cycles, and the boiler’s oversized capacity necessitates using a VSD to adjust fan motor speed and reduce energy consumption.
This study highlights the significant energy and cost savings achievable through simple, well-known conservation measures. It emphasizes optimizing excess air and stack temperature in boiler operations.
Stack Gas Heat Losses
The most significant energy losses in oil-fired boilers occur through the chimney, driven by the temperature and volume of exhaust gases. While some heat loss is unavoidable, minimizing excess air and reducing stack gas temperature can significantly improve efficiency. This study focuses on three key strategies to reduce stack gas losses:
- Minimizing excess air,
- Optimizing combustion conditions and
- Implementing variable speed control for fan motors.
Excess Air Control
To ensure complete combustion and safe operation, boilers require more air than theoretically necessary. However, excessive air increases energy losses. This study evaluates three methods for controlling airflow:
- Inlet damper control,
- Inlet vane control and
- Variable speed control.
Among these, variable speed control offers the most precise and energy-efficient solution, allowing fan motors to operate at speeds tailored to load requirements.
Variable Speed Control System
Variable speed drives (VSDs) adjust motor speed by varying the electrical supply frequency. This method provides precise motor torque and speed control, saving energy significantly. By reducing fan motor speed from 1450 rpm to 400 rpm during low-load conditions, the study achieved a 2.5% increase in boiler efficiency and substantial electrical energy savings.
Electrical Energy Savings Calculation
The 30 kW fan motor in the study operated at full speed six days a week, totaling 8760 hours annually. However, much of this operation was unnecessary, as the motor often ran at full speed even during low-load conditions. By implementing a VSD, the motor’s speed was adjusted based on real-time load requirements, resulting in significant energy savings. Tables 3 and 4 illustrate the power consumption before and after VSD implementation, highlighting the potential for cost and energy savings.
Conclusion
Applying a variable speed drive to a boiler fan motor can save energy and cost. By optimizing the fan motor speed based on load requirements, the boiler system achieved a 2.5% efficiency improvement and saved 8000 kWh of electricity per month. These findings underscore the importance of adopting simple, cost-effective measures to enhance boiler efficiency, reduce energy waste, and contribute to global efforts to mitigate climate change.
“We greatly appreciate you taking the time to read our article! “Maximizing Efficiency: Energy Conservation with Variable Speed Controllers in Boiler Houses.” To help us reach a wider audience and continue creating valuable content, we kindly ask that you like and share this article on your preferred social media platforms. Your feedback is also invaluable. Please take a moment to leave a comment below, sharing your thoughts and insights on the article in 100 words or less. Your input helps us understand what resonates with our readers and allows us to improve our future content.”