Cooling Water System Commissioning: A Comprehensive Overview
Introduction
In industrial and commercial facilities, cooling water systems are critical for maintaining operational efficiency and ensuring the longevity of vital equipment. These systems, encompassing components such as cooling towers, pumps, and heat exchangers, require meticulous planning and execution to function optimally. A crucial step in this process is commissioning, a systematic procedure that verifies the cooling water system’s proper design, installation, and operation. This article provides a comprehensive overview of the commissioning process, emphasizing its significance and outlining key considerations for successful implementation.
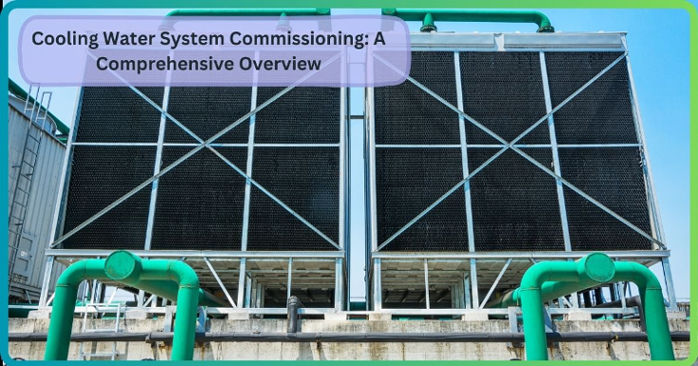
The Importance of Commissioning Cooling Water Systems
Effective cooling water system commissioning offers numerous benefits:
- Enhanced System Performance: Commissioning ensures the system operates at peak efficiency, maximizing cooling capacity and minimizing energy consumption.
- Early Detection of Issues: By rigorously testing each component and the system, potential problems can be identified and addressed proactively, preventing costly downtime and repairs later.
- Improved Reliability and Longevity: A properly commissioned system is more likely to operate reliably over its lifespan, reducing the frequency of maintenance interventions and extending the equipment’s service life.
- Enhanced Safety: Commissioning procedures prioritize safety by identifying and mitigating potential hazards, such as leaks, electrical faults, and chemical imbalances.
- Compliance with Standards: A well-documented commissioning process demonstrates adherence to industry practices and relevant regulations, which can be crucial for obtaining permits and ensuring compliance.
Key Stages in the Commissioning Process
The commissioning process typically involves several distinct stages:
- Pre-Commissioning: This initial phase focuses on pre-operational checks, including:
- Visual Inspection: All system components are thoroughly inspected to identify any physical damage, misalignments, or other anomalies.
- Leak Detection: Piping and equipment connections are meticulously checked for leaks to prevent water loss and potential damage.
- Control System Verification: The control system, including sensors, actuators, and programmable logic controllers (PLCs), is tested to ensure proper functionality and communication.
- Start-up and Initial Operation:
- System Start-up: The cooling water system is carefully started, following manufacturer guidelines and established procedures.
- Performance Monitoring: Key performance parameters, such as flow rates, temperatures, and pressures, are continuously monitored and recorded during initial operation.
- Functional Performance Testing:
- Load Testing: The system is subjected to varying load conditions to evaluate its performance under different operating scenarios.
- Efficiency Analysis: Energy consumption is monitored and analyzed to identify areas for improvement and optimize system efficiency.
- System Optimization:
- Fine-tuning: Based on the data collected during testing, adjustments are made to system parameters, such as flow rates and control settings, to optimize performance and efficiency.
- Troubleshooting and Corrective Actions: Any identified issues or deficiencies are addressed through appropriate corrective actions, such as repairs, modifications, or adjustments.
- Commissioning Documentation:
- Record Keeping: Detailed records, including test results, observations, and corrective actions, are maintained throughout the commissioning process.
- Commissioning Report: A comprehensive commissioning report is prepared, documenting the entire process and summarizing the findings and conclusions.
Flushing and Passivation
A thorough flushing procedure is implemented to ensure system cleanliness. During construction, debris may accumulate within the cooling water pipelines and basin. To remove these particles, the system undergoes a rigorous flushing process. The cooling tower basin is flushed by opening the blowdown valve. Following erection, the pipeline leading to the condenser is hydrostatically tested. The test water is subsequently drained. Further flushing is conducted using either the primary cooling water pump or a temporary pump with a dedicated looping arrangement if necessary.
After thorough flushing, the pipeline is connected to the condenser. Cooling water is circulated through the condenser tubes for several days to facilitate passivation. This process promotes the formation of a protective layer on the inner surface of the condenser tubes, enhancing their corrosion resistance and extending their service life.
Practices for Successful Commissioning
To ensure the success of the cooling water system commissioning process, several practices should be followed:
- Experienced Personnel: Engage experienced commissioning professionals with expertise in cooling water systems and relevant industry standards.
- Detailed Planning: Develop a comprehensive commissioning plan that outlines the scope of work, schedule, and responsibilities of all parties involved.
- Use of Modern Tools: To enhance data collection and analysis, utilize advanced technologies, such as data loggers, infrared cameras, and computerized maintenance management systems (CMMS).
- Collaboration and Communication: Foster effective communication and cooperation between the design team, contractors, and facility operators throughout the commissioning process.
- Continuous Improvement: Regularly review and refine commissioning procedures based on lessons learned from past projects and industry practices.
Conclusion
By adhering to a rigorous commissioning process, facility owners and operators can ensure that their cooling water systems operate efficiently, reliably, and safely. This contributes to significant energy savings and reduced operating costs, enhancing the facility’s overall sustainability and environmental performance. By embracing a proactive approach to cooling water system commissioning, organizations can maximize the return on their investment in critical cooling infrastructure.
Disclaimer: This article provides general information and should not be considered professional engineering advice. The specific requirements and procedures for commissioning cooling water systems may vary depending on the application, local regulations, and industry standards. It is essential to consult with qualified professionals and adhere to relevant codes and standards for all commissioning activities.
We greatly appreciate you taking the time to read our article! “Cooling Water System Commissioning: A Comprehensive Overview” To help us reach a wider audience and continue creating valuable content, we kindly ask that you like and share this article on your preferred social media platforms. Your feedback is also invaluable. Please take a moment to leave a comment below, sharing your thoughts and insights on the article in 100 words or less. Your input helps us understand what resonates with our readers and allows us to improve our future content.”