The Invisible Force: Control & Instrumentation in Power Plants
Introduction
Control and Instrumentation (C&I) systems are integral to the operation of any process plant. They serve as the plant’s nervous system by monitoring and controlling various processes. In the context of power plants, C&I systems are crucial for ensuring safe and efficient power generation.
Instrumentation involves measuring process variables such as pressure, temperature, and flow. These measurements provide operators with real-time data on the plant’s performance. Conversely, control engineering uses this data to maintain desired operating conditions through automated adjustments. This integration of instrumentation and control enables the automation of various functions within a power plant, enhancing operational efficiency and reliability.
Modern power plants employ advanced systems such as Distributed Control Systems (DCS) and Programmable Logic Controllers (PLC) to achieve high levels of automation. These systems facilitate precise process control, improving the plant’s safety and performance.
While the full scope of C&I systems is extensive, this chapter aims to provide power plant engineers with a foundational understanding of their functions and significance. A solid grasp of C&I principles is essential for effective plant operation and maintenance, as these systems play a pivotal role in monitoring and controlling the complex processes inherent in power generation.
The Role of Control and Instrumentation in Power Plants
Control and instrumentation systems are pivotal in monitoring and regulating various parameters within a power plant. These systems involve measuring instruments, controllers, and actuators that work together to:
- Ensure Operational Safety: Power plants handle hazardous materials and operate under extreme conditions. C&I systems monitor critical parameters like temperature, pressure, and flow to ensure safe operations.
- Optimize Efficiency: Energy production must be efficient to minimize fuel consumption and environmental impact. Control systems fine-tune processes to achieve optimal performance.
- Enable Automation: Modern power plants are highly automated, reducing the need for manual intervention. Advanced C&I technologies power this automation.
- Facilitate Data Analysis: Real-time sensor data provides insights into plant performance, aiding predictive maintenance and decision-making.
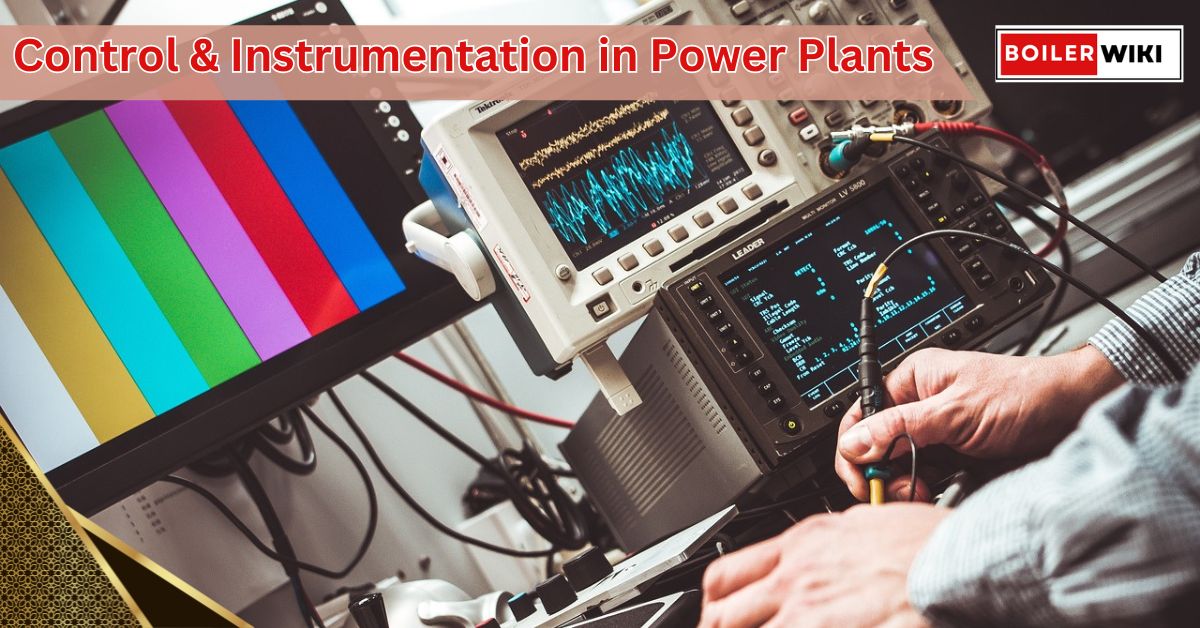
Key Components of Control and Instrumentation Systems
The C&I framework in a power plant is a complex network of devices and systems. Let’s explore some key components:
1. Sensors and Transducers
These devices convert physical quantities like temperature, pressure, or flow into measurable electrical signals.
- Thermocouples measure temperature.
- Pressure transducers monitor steam and fluid pressure.
- Flow meters track the movement of liquids and gases.
2. Controllers
Controllers process data from sensors to maintain desired setpoints. They use algorithms like Proportional-Integral-Derivative (PID) control to make precise adjustments. For example, a boiler temperature controller ensures the steam temperature remains within safe limits.
3. Actuators
Actuators execute commands from controllers by physically adjusting equipment. Examples include:
- Valves that regulate fluid flow.
- Dampers that control airflow in ducts.
- Motors that drive machinery.
4. Supervisory Control and Data Acquisition (SCADA) Systems
SCADA systems provide centralized monitoring and control of the entire plant. Operators use SCADA interfaces to visualize real-time data, issue commands, and analyze trends.
5. Distributed Control Systems (DCS)
DCS divides the control tasks across multiple processors, making the system more reliable and scalable. This is beneficial in large power plants with numerous control tasks.
6. P and I Diagram
The p and I diagram is an essential drawing for process measurement and control. This diagram shows the pipeline, installed equipment, instrumentation, and control interlocks. This is a schematic drawing to show the process flow and its power.
A standard set of symbols is used to represent all the components. All the components of a P and I diagrams are identified by numbering systems. This unique item number can quickly identify every equipment, valve, instrument, and pipeline. The pipeline number contains its size, thickness, material, and fluid contents. Some suitable symbols can also identify the location of instruments and their type. In a power plant, the following process parameters are measured:
• Pressure
• Temperature
• Flow
• Level
• Weight
• Vibration
• Speed
7. MEASUREMENT OF PRESSURE
In a power plant, it is required to measure the pressure of steam, water, air, etc. Pressure gauges are used for this measurement. Pressure transmitters are used for process control and measurement in distributed control systems (DCS) and programmable logic control (PLC)systems. Various principles are used for pressure measurement. Bourdon tube and manometer are two essential principles used for pressure measurement.
- Bourdon Tube Pressure Gauge
- Manometer
- Pressure Sensor/Transmitter
- Smart Transmitter
8. MEASUREMENT OF TEMPERATURE
The measurement of temperature is an essential function of a power plant. It is required to measure the temperature of feedwater, steam, flue gas, air, etc., at various points. Temperature is a critical parameter in knowing the condition of the process. Multiple techniques are used to measure temperature. Like pressure measurement, Temperature measurement has two main elements: sensor and transmitter. The sensor is exposed to a hot fluid whose temperature will be measured. A sensor uses the following principles:
• Thermocouple (TC)
• Resistance temperature device (RTD)
• Liquid expansion and vapor pressure
• Bimetallic
• Infrared
• Pyrometer
9. MEASUREMENT OF FLOW
In power plants, it is required to measure the flow of fluids like cooling water, feedwater, steam, air, etc. Various types of flow meters are used for this. Some of the common types are given below:
• Mechanical flow meter
• Differential flow meter
• Electromagnetic flow meter
• Ultrasonic flow meter
• Rotameter
10. MEASUREMENT OF THE LEVEL OF LIQUID
Level measurement is one of the critical process measurements. Measuring the level of various liquid and solid materials is required in a power plant. Level of liquids like water tank, DM water tank, condenser hot well, deaerator, and solids like coal bunker, ash hopper, etc. Are measured. In this section, we will discuss the level measurement of liquid. The level measurement of liquid is of two types—direct and indirect.
The Evolution of Control and Instrumentation Technologies
The field of control and instrumentation has evolved significantly, driven by advancements in technology:
1. Digital Transformation
Traditional analog systems have given way to digital solutions, offering higher accuracy and reliability. Digital sensors, smart controllers, and software-driven systems dominate modern power plants.
2. Internet of Things (IoT)
IoT devices enable seamless communication between components, enhancing real-time monitoring and predictive maintenance.
3. Artificial Intelligence and Machine Learning
AI-powered analytics predict equipment failures and optimize plant operations by analyzing historical and real-time data.
4. Cybersecurity
Protecting power plants from cyber threats has become a priority as they become more connected. Advanced C&I systems incorporate robust cybersecurity measures to safeguard critical infrastructure.
Conclusion
While the towering turbines and colossal boilers might capture the imagination, the intricate interplay of “control and instrumentation systems” truly orchestrates the symphony of a power plant. These “invisible forces” – the sensors, transmitters, and controllers – diligently monitor every aspect of plant operation, ensuring safe, efficient, and reliable energy production. From regulating temperatures and pressures to optimizing fuel consumption, these systems are the unsung heroes that maintain the delicate balance within the power plant ecosystem. As technology advances, we can expect even more sophisticated control systems to emerge, further enhancing the efficiency and sustainability of power generation.
“We greatly appreciate you taking the time to read our article!“The Invisible Force: Control & Instrumentation in Power Plants” To help us reach a wider audience and continue creating valuable content, we kindly ask that you like and share this article on your preferred social media platforms. Your feedback is also invaluable. Please take a moment to leave a comment below, sharing your thoughts and insights on the article in 100 words or less. Your input helps us understand what resonates with our readers and allows us to improve our future content.”