Cold Startup Process of WHRB (Waste Heat Recovery Boiler)
The WHRB boiler is commissioned with a very carefully orchestrated cold start-up procedure. During this crucial period, close familiarity with the inner workings of the complex systems in the boiler, and strict adherence to safety procedures is required. All components such as valves and gauges, safety devices were thoroughly examined before a pre-start inspection of a WHRB boiler is carried out.
Following this, a phased method is employed, in which the boiler drum and other piping systems are sequentially pressurized. During this time, it is essential to constantly monitor a host of critical parameters (pressure, temperature, water levels, etc.) to avoid any surprises.
Starting up a WHRB boiler requires ramping up burner firing rates and careful balancing of air and fuel ratios. Such a balancer has to say right above combustion in efficiency and to minimize the risk of thermal stress on the structural integrity of the boiler. Simulation and testing of boiler control systems to ensure responsiveness to changing conditions. This prepares the Waste Heat Recovery Boiler (WHRB) to carry out its core function with utmost safety without wear and maximizing efficiency. Follow this guide, step by step:
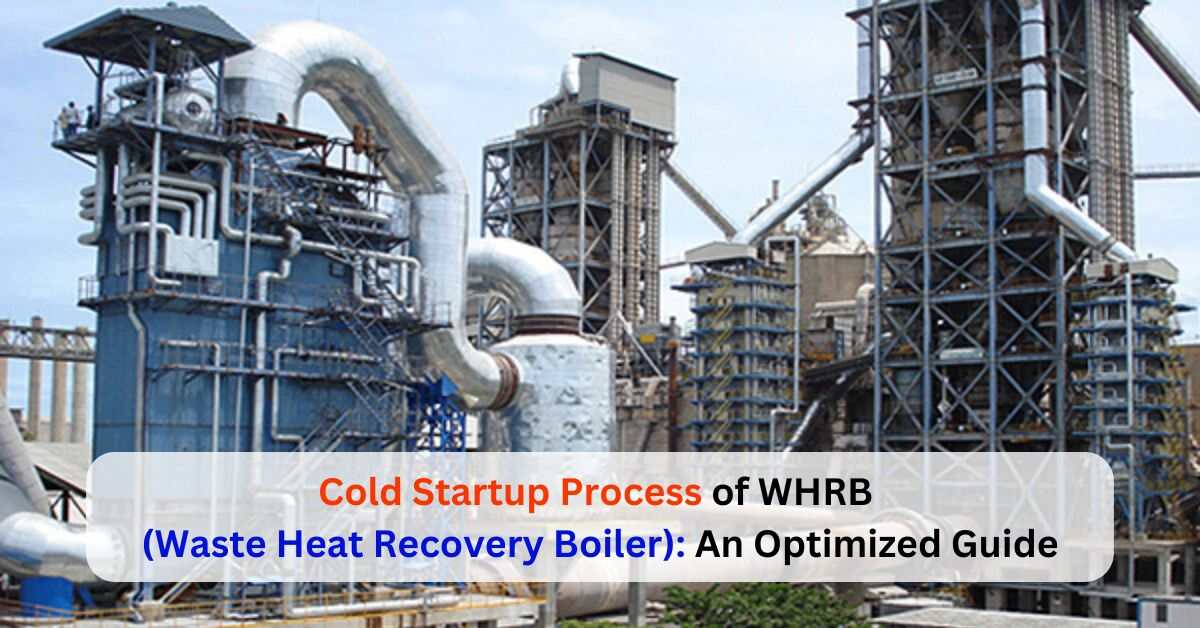
Step-by-Step Process for WHRB Cold Startup
1. Startup with Kiln Light-Up
After ignition of kiln and at a flue gas temperature at the PCC outlet of over 450°C open the ID fan damper to 5%. Use the natural draft of the stack pulls flue gas through the boiler, and started heating slowly, expansion.
2. Gradual Temperature Increase
Be watchful as the temperature of the burner of the boiler raises. Increase the ID fan damper 10% at250°C for line by line heating after the furnace reaches the250°C.
3. Starting the ID Fan
When id fan damper is closed according to draft control, open id fan to control environmental conditions, id fan started 600°C on the flue gas temperature of PCC outlet.
4. Managing Drum Pressure
At 5 kg/cm² drum pressure, close the drum vent and puppy header vent to pressure hold.
5. Blowdown for Maintenance
As soon as the drum pressure arrives at 20 kg/cm² blow down the water walls in the drum to clean any sludge and deposit formation and improve the conductivity and efficiency. Boiler Pressure Increasing Process: Open the dampers steadily to increase the boiler pressure to 45 kg/cm² and attain a temperature of 485°C; the startup vent should remain open in order to allow for the adjustment of the admittance of hot flue gas.
6. Steam Line Preparations
To blow down condensate, opens the main steam line drains (MSSV to TG MSSV) Do the MSSV bypass open to remove all notion in the main steam line. Ensure the TG MSSV stays closed throughout this process.
7. Main Steam Valve Operations:
Open the MSSV to the boiler and close the superheat drains after condensate and line heating.
8. Automating Controls
Put the drum level controller and attemperator controller to Auto Mode for accurate operation.
“We greatly appreciate you taking the time to read our article! “Cold Startup Process of WHRB (Waste Heat Recovery Boiler)” To help us reach a wider audience and continue creating valuable content, we kindly ask that you like and share this article on your preferred social media platforms. Your feedback is also invaluable. Please take a moment to leave a comment below, sharing your thoughts and insights on the article in 100 words or less. Your input helps us understand what resonates with our readers and allows us to improve our future content.”