Boiler Commissioning: Why It’s Important and How It Works
Introduction
Boilers are indispensable in industrial and residential settings, serving as the backbone for heating systems, power generation, and various manufacturing processes. These complex systems operate under high pressure and temperature, making their safety and efficiency paramount. Before a boiler can begin regular operation, it must undergo a meticulous process known as boiler commissioning. Simply put, boiler commissioning involves preparing, inspecting, testing, and fine-tuning a boiler to ensure it functions optimally and adheres to safety and performance standards.
This article aims to provide a comprehensive understanding of boiler commissioning. We will delve into its steps, highlight its significance, and address common challenges encountered during the process. By the end, you’ll appreciate why boiler commissioning is critical for ensuring reliable and efficient operation.
What is Boiler Commissioning?
Boiler commissioning is the systematic procedure of validating a boiler’s functionality before it becomes operational. This process involves thorough inspections, detailed testing, and precise adjustments to ensure the system operates safely and efficiently.
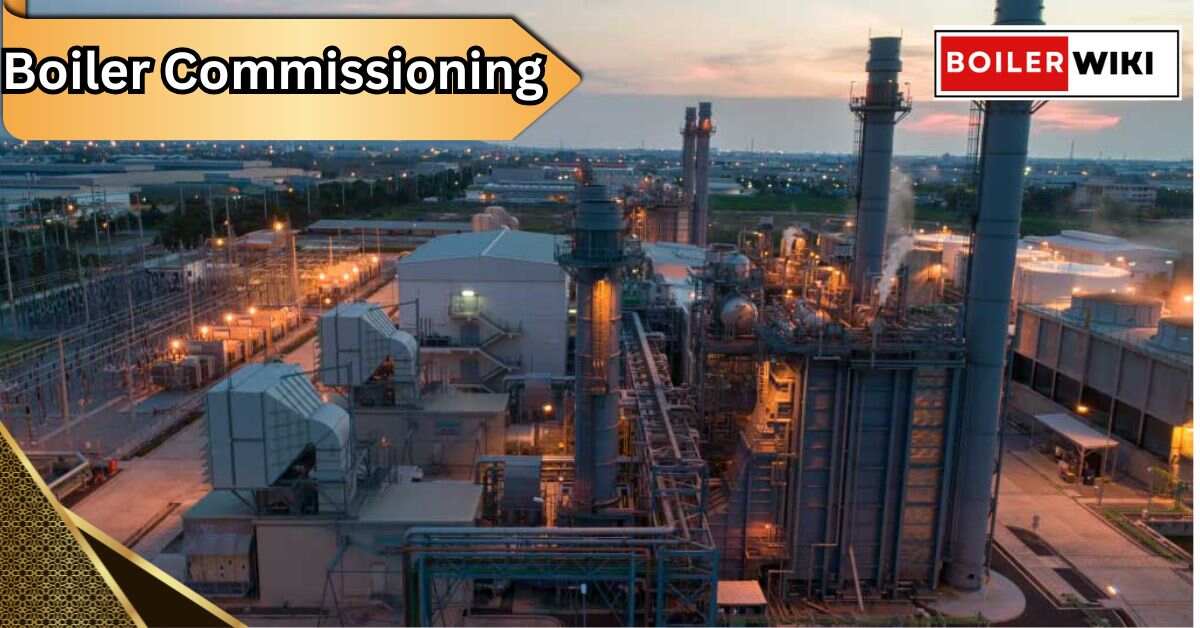
Commissioning ensures compliance with regulatory standards and surties optimal performance, whether for a newly installed boiler or a unit undergoing significant repairs or upgrades.
Steps in Boiler Commissioning
Leakage Test of Pressure Parts and Flushing
Extensive welding work is performed during the erection of boiler pressure parts. X-ray tests are conducted on selected joints to ensure the quality of these welds. X-ray testing is not only essential for quality assurance but is also mandated by statutory regulations. Typically, a percentage of the total welded joints undergo an X-ray examination, as testing every joint is not feasible. Consequently, there remains a possibility of undetected welding defects in some joints.
The pressure parts are initially filled with water using a small-capacity pump to identify potential defects. Deionized (DM) water is employed for this purpose. Any leaks from defective welds are simple detectable during this process and can be promptly rectified.
Hydrostatic Pressure Test of Pressure Parts
A hydro test of a newly erected boiler is a statutory requirement. It can also detect any minor leakage in the pressure part. The procedure of the hydro test is already discussed in the earlier chapters. In the case of a new boiler, the hydro test must be carried out carefully. The pressure is to be raised slowly, and if any leakage is found, this is to be arrested.
Furnace Leakage Test
The boiler furnace comprises water walls, castable materials, refractories, and solid plates. It is critical to ensure that flue gases do not leak from the stove and that atmospheric air does not enter the boiler. Due to the extensive welding required to construct this area, leakage is always possible. Before the boiler’s initial firing, it is essential to confirm no leaks in the furnace or the flue gas path.
A simple test is conducted to identify leaks. All doors and dampers are sealed, and smoke is generated inside the furnace. After a short period, any leaks in the flue gas path can be detected as smoke escapes through them. These points are then identified and sealed. Alternatively, a light can be placed inside the furnace and flue gas path while the external boiler area is darkened. If leaks are present, the light will shine through, making them visible.
Chemical Cleaning of Pressure Parts
Oil, grease, iron oxide (rust), and mill scale are present in the pressure parts of a newly erected boiler. Pressure parts must be cleaned thoroughly before the boiler is put in service. Otherwise, these particles will affect the heat transfer and create problems in the circulation of feedwater inside the boiler. For this purpose, chemical cleaning of the boiler pressure parts is carried out.
Acid Cleaning
Acid cleaning is done by either the circulation or fill-and-soak method. The circulation method is preferred to clean the pressure parts of natural or forced circulation boilers. Here, we will discuss a new boiler’s acid-cleaning and passivation procedure. The procedure is almost the same in both cases, with a little difference in the monitoring parameters. Most pressure parts in a new boiler are connected to an acid-cleaning circulation-type arrangement. The acid solution is prepared in the acid solution tank. The temporary pipeline is fabricated to circulate the acid in the boiler pressure parts. The arrangement is so made that all the drainable pressure parts are connected for acid circulation. Sometimes, the main steam pipeline is also included in the loop.
EDTA Cleaning
Ethylenediaminetetraacetic acid (EDTA) is used extensively to clean boilers nowadays. EDTA is circulated in the boiler pressure parts to clean the boiler tube’s inside surface. The solution’s circulation occurs due to the natural circulation of water during the controlled operation of the boiler, like alkali boil-out. Cleaning, neutralization, and passivation can be achieved sequentially with a single solution under controlled conditions. Hence, the cleaning and passivation time reduces drastically.
Safety Valve Setting
Safety valve setting is a statutory requirement. As discussed earlier, there are three safety valves. One is installed at the superheater outlet, and the other two are placed at the steam drum. A superheater safety valve is set at a lower pressure than the drum safety valves. To put these safety valves, the boiler is lighted up. The safety valve to be set is kept on service, and the other two are gagged. Pressure on the boiler is raised slowly per the standard boiler operation procedure. The fuel feeding rate is kept at a minimum.
The safety valve is required to lift and reset at a desired pressure as per the boiler pressure rating. Accordingly, it is adjusted to get the lift and reset pressure. Like this, all three safety valves are set. All the gagging is removed. Percussion is to be taken during initial pressure build-up. The drum pressure gauge should be perfect and calibrated. If the safety valve does not lift beyond the set pressure, the boiler’s pressure will be reduced, and the setting will be repeated.
Commissioning of Boiler Feed Pump
Before commissioning any equipment in a power plant, the electric motor of that equipment should be commissioned first. The direction of rotation and the current drawn should be checked. The motor should be left to run on no load for some time in decouple condition. Only then should coupling be done.
Special care should be taken while commissioning a boiler feed pump. The deaerator should be inspected and cleaned thoroughly to avoid foreign particles on the feed pump suction line. The pump suction strainer should be cleaned. Cooling water should flow independently for gland and bearing cooling. The bearing should be adequately lubricated, and the pump should be appropriately aligned with the motor.
The feed pump is to be started locally for the first time. Pump body temperature and any abnormal sound, bearing temperature, motor current, discharge pressure, balancing pressure, etc., must be checked regularly.
Commissioning of Fuel Handling System
Like other power plant drives, drives used for fuel handling, such as belts, crushers, screens, oil pumps, etc., must be commissioned individually. The safety interlocks are to be checked. There should not be any oil/gas leakage from the fuel pipeline. For a coal-fired boiler, the system, as a whole, should run perfectly with all the interlocks. The weigh feeder should indicate the accurate weight. Crusher, screen, elevator, etc., are to be commissioned individually.
Other auxiliary systems of the boiler, such as the ash handling system, ESP, etc., must be commissioned before the boiler is put into operation.
Why is Boiler Commissioning Important?
The importance of boiler commissioning cannot be overstated. Proper Commissioning:
- Ensures Safety: Boilers operate under high pressure and temperature, prioritizing safety. Commissioning identifies potential hazards and mitigates risks.
- Optimizes Performance: Commissioning ensures energy-efficient operation by calibrating the boiler and its components, reducing fuel consumption and operating costs.
- Prolong Equipment Life: Detecting and addressing issues early prevents wear and tear, extending the boiler’s lifespan.
- Compliance with Regulations: Boilers must meet strict safety and environmental standards. Commissioning ensures adherence to these regulations.
- Minimizes Downtime: A well-commissioned boiler is less likely to encounter operational disruptions, ensuring consistent performance.
Conclusion
Boiler commissioning is critical in ensuring the safe and efficient operation of boilers. By understanding its importance and the steps involved, operators can maximize performance, extend equipment life, and ensure safety and environmental standards compliance. As the energy landscape continues to evolve, staying informed about advancements in boiler technology and commissioning practices will remain essential. Proper boiler commissioning lays the foundation for reliable and sustainable energy solutions for industrial applications or heating systems.
“We greatly appreciate you taking the time to read our article!“Boiler Commissioning: Why It’s Important and How It Works” To help us reach a wider audience and continue creating valuable content, we kindly ask that you like and share this article on your preferred social media platforms. Your feedback is also invaluable. Please take a moment to leave a comment below, sharing your thoughts and insights on the article in 100 words or less. Your input helps us understand what resonates with our readers and allows us to improve our future content.”