A Simple Guide to Turbine Commissioning
Introduction
Turbines are mechanical devices that convert kinetic energy from fluids—such as wind, water, steam, or gas—into mechanical energy, which is often further transformed into electrical power. They are pivotal components in power generation systems, ranging from wind farms to thermal power plants. The commissioning of turbines is the final phase that ensures these machines are prepared to produce energy efficiently and safely.
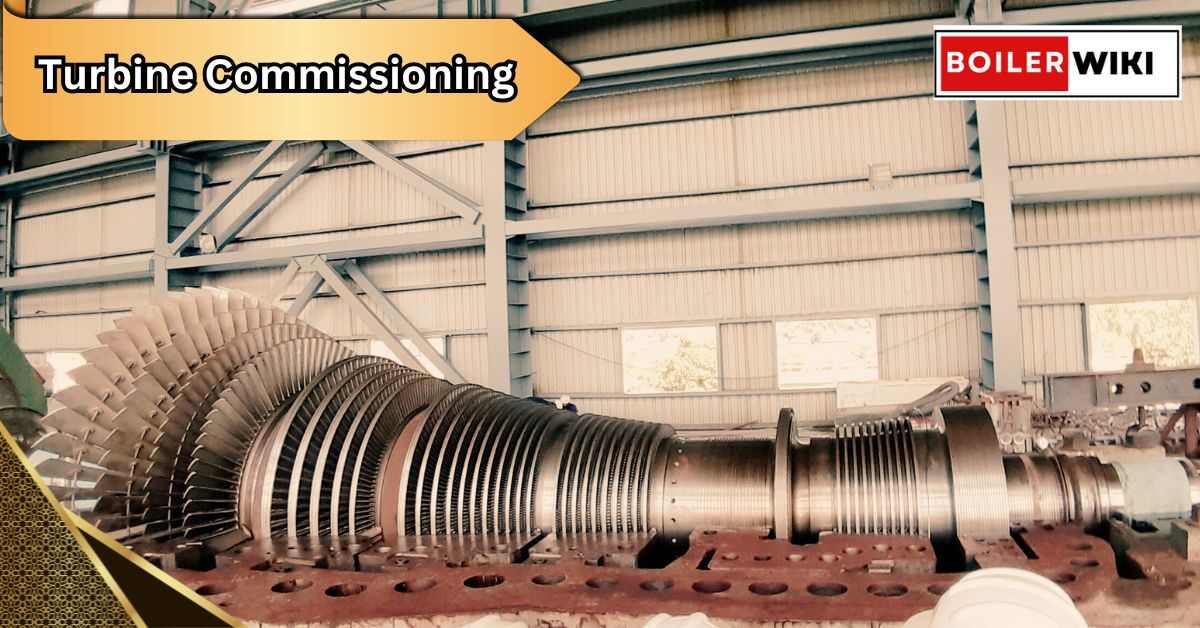
This process involves a series of meticulous tests and validations to confirm that the turbine operates by its design specifications and performance criteria. Understanding how these colossal machines commence their energy production journey offers valuable insights into the complexities of modern power generation.
Understanding Turbine Commissioning
Commissioning is a systematic process that transitions a turbine from installation to full operational status. It encompasses a series of inspections, tests, and adjustments to verify that all components function correctly and cohesively. The primary objectives of commissioning include:
- Safety Assurance: Confirm that the turbine operates without harming personnel or the environment.
- Performance Validation: Ensuring the turbine meets the expected efficiency and output levels.
- Reliability Verification: Establish that the turbine can operate consistently over its lifespan.
A well-executed commissioning process is essential for optimizing the turbine’s performance and longevity, thereby maximizing the return on investment for stakeholders.
Key Steps in the Commissioning Process
The commissioning of turbines involves several critical stages, each tailored to the specific type of turbine—wind, steam, or gas. While the exact procedures may vary, the general steps include:
- Lube Oil Flushing
- Steam Blowing
- Turbine on Barring
- Commissioning of Condensate System
- Rolling of Turbine
- Overspeed Test
1. Lube Oil Flushing
Lubricating oil is essential for turbine operation, bearings, and other critical components. To prevent damage from contaminants such as rust, dust, or welding debris introduced during fabrication, the lubrication system must be cleaned thoroughly before the turbine becomes operational. This is achieved through lube oil flushing, a crucial step in turbine commissioning.
The lube oil flushing procedure typically involves several key steps:
- System Preparation: Ensure that the main oil tank (MOT), coolers, filters, and piping systems are completely drained of any existing oil. Thoroughly clean the MOT internals using appropriate cleaning tools and compressed air. After cleaning, fill the MOT with fresh, filtered lube oil of the recommended grade, ensuring the oil level meets operational requirements.
- Temporary Bypass Installation: To prevent contaminants from reaching sensitive components, install temporary bypass lines across bearing housings and seal oil supplies. This setup allows oil to circulate through the entire pipeline without entering the bearings. Remove orifices, probes, and other flow restrictions to achieve optimal flow velocities during flushing.
- Initial Oil Circulation: Start the auxiliary oil pump to circulate oil through the system. During this phase, avoid allowing oil to enter the turbine bearings. Monitor for any leaks and address them promptly. Install a fine mesh (e.g., 100-micron stainless steel) in the return line to the oil tank to capture debris. Regularly inspect and clean this mesh to assess the system’s cleanliness.
2. Steam Blowing
Steam blowing is crucial for cleaning the main steam pipeline connected to a turbine. High-velocity steam dislodges particles within the boiler and piping system, preventing damage to the turbine’s internal components. This process involves subjecting the pipeline to thermal cycling (rapid heating and cooling) and high-pressure steam flow, which dislodges mill scale and weld slag from the pipe walls. Steam flow during blowing should match or exceed regular operation at maximum load for optimal cleaning.
However, steam blowing creates extreme conditions, including rapid temperature changes that can cause thermal stress in critical components like steam drums, headers, and piping. Therefore, careful planning and execution are essential. Before steam blowing, the pipeline undergoes thorough preparation. This typically includes a hydraulic test, followed by flushing with water. In some cases, chemical cleaning with an acid solution may be performed, followed by thorough rinsing.
The pipeline is connected to the turbine’s extraction steam valve (ESV) for the steam-blowing process. The ESV is removed, and a temporary pipe is connected to vent steam to the atmosphere. This setup, often illustrated in diagrams, allows for controlled steam release and ensures effective cleaning of the entire pipeline.
3. Turbine on Barring
Rotating a turbine for the first time using a barring device requires utmost care. Due to the tight turbine clearances, improper alignment with the gearbox or generator can cause significant damage during barring.
Before barring, ensure proper turbine internal clearances and alignment per the manufacturer’s recommendations. Start lube oil circulation and, if available, manually rotate the rotor. Check the barring gear motor’s rotation in a decoupled state. Prepare the oil supply line for hydraulic barring.
Set bearing oil pressure as per requirements. After coupling the barring gear motor, start the device and monitor for abnormal sounds, vibrations, or rising bearing temperature at regular intervals. If all checks are routine, the turbine can be barred for a specific duration before starting.
4. Commissioning of Condensate System
Before commissioning, the condensate system, including the condenser, pipelines, and deaerator, requires thorough cleaning. This removes foreign particles like dust, welding debris, and even inadvertently left tools.
To check for leaks, the condenser is filled with demineralized (DM) water. In some cases, a hydraulic test is performed on the shell side.
After flushing, water is circulated through the condensate extraction pumps (CEPs), bringing all connected systems (LP heater, gland steam condenser, main ejector condenser) online. CEPs are tested individually, and all interlocks are checked.
During initial turbine operation, dislodged scale and rust can choke the CEP suction filter. Therefore, regular differential pressure monitoring across the suction strainer is crucial until the system stabilizes.
5. Turbine Rolling
Before rolling, activate the barring gear and commission all auxiliary systems. Initiate turbine heating with all casing drains open. After proper line heating, steam is introduced to the extraction steam valve (ESV). Record the position of the main steam line support hangers in both cold and hot conditions. Adjust hanger loading as needed.
Roll the turbine in manual or semi-auto mode, allowing sufficient time for rotor socking. Monitor casing and rotor expansion to ensure unrestricted casing expansion. Carefully monitor parameters like bearing temperature, vibration, exhaust pressure, and temperature at lower speeds. Gradually increase speed, exercising extreme caution during critical speed bands.
Key Points
- Thorough system checks and preparations are crucial before rolling.
- Controlled steam introduction and gradual speed increase are essential.
- Close monitoring of critical parameters is vital throughout the process.
- Special attention must be paid to crucial speed ranges to avoid potential issues.
6. Overspeed Test
The overspeed test is crucial for setting the turbine’s overspeed trip limit. After thoroughly rolling the turbine and ensuring proper heating, the turbine’s speed gradually increases.
The governor controls speed up to the maximum governing limit. If an electrical overspeed trip is present, it’s bypassed for testing.
Further increasing speed activates the mechanical overspeed trip device. Centrifugal force disengages a pin on the rotor, triggering the trip lever. The trip limit is adjusted by adjusting a spring’s tension.
Completing the mechanical overspeed test and setting prepares the turbine for loading.
Key Points:
- Thorough turbine heating is essential before the test.
- Governor control is crucial up to the maximum governing speed.
- Electrical overspeed trips are bypassed for testing.
- Mechanical overspeed trip operation is verified and adjusted.
- Successful completion ensures safe turbine operation.
Conclusion
Turbine commissioning is a multifaceted process vital in successfully deploying power generation systems. By systematically verifying each component and system, commissioning ensures that turbines operate safely, efficiently, and reliably. This comprehensive approach safeguards significant financial investments and contributes to sustainable and dependable energy production. As the energy sector continues to evolve, the principles and practices of effective turbine commissioning remain fundamental to meeting the world’s growing power demands.
“We greatly appreciate you taking the time to read our article!“A Simple Guide to Turbine Commissioning” To help us reach a wider audience and continue creating valuable content, we kindly ask that you like and share this article on your preferred social media platforms. Your feedback is also invaluable. Please take a moment to leave a comment below, sharing your thoughts and insights on the article in 100 words or less. Your input helps us understand what resonates with our readers and allows us to improve our future content.”